How can recalls be prevented?
Among many solutions, one very interesting solution is to integrate and unify all tightening data into a single database, supported by a comprehensive automated analytics system, including data from suppliers. This unified approach facilitates: Better control, deeper insights and proactive problem-solving. Still not convinced. Let’s consider a concrete example.
Data analysis and data collection: the keys to a successful recipe! 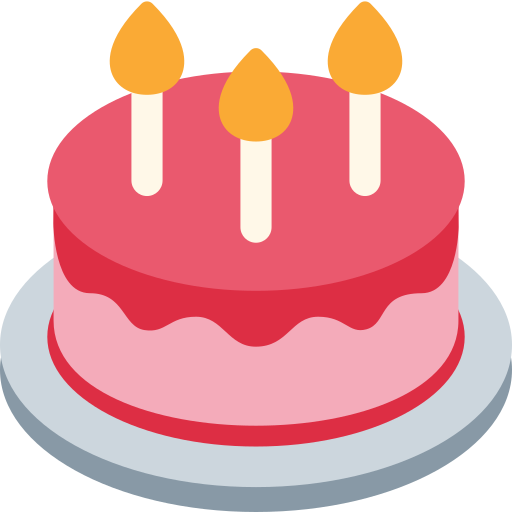
Imagine operating a bakery without utilising data-driven solutions. It's akin to baking a cake without a recipe. You might occasionally create a masterpiece, but more often, you'll encounter significant issues:
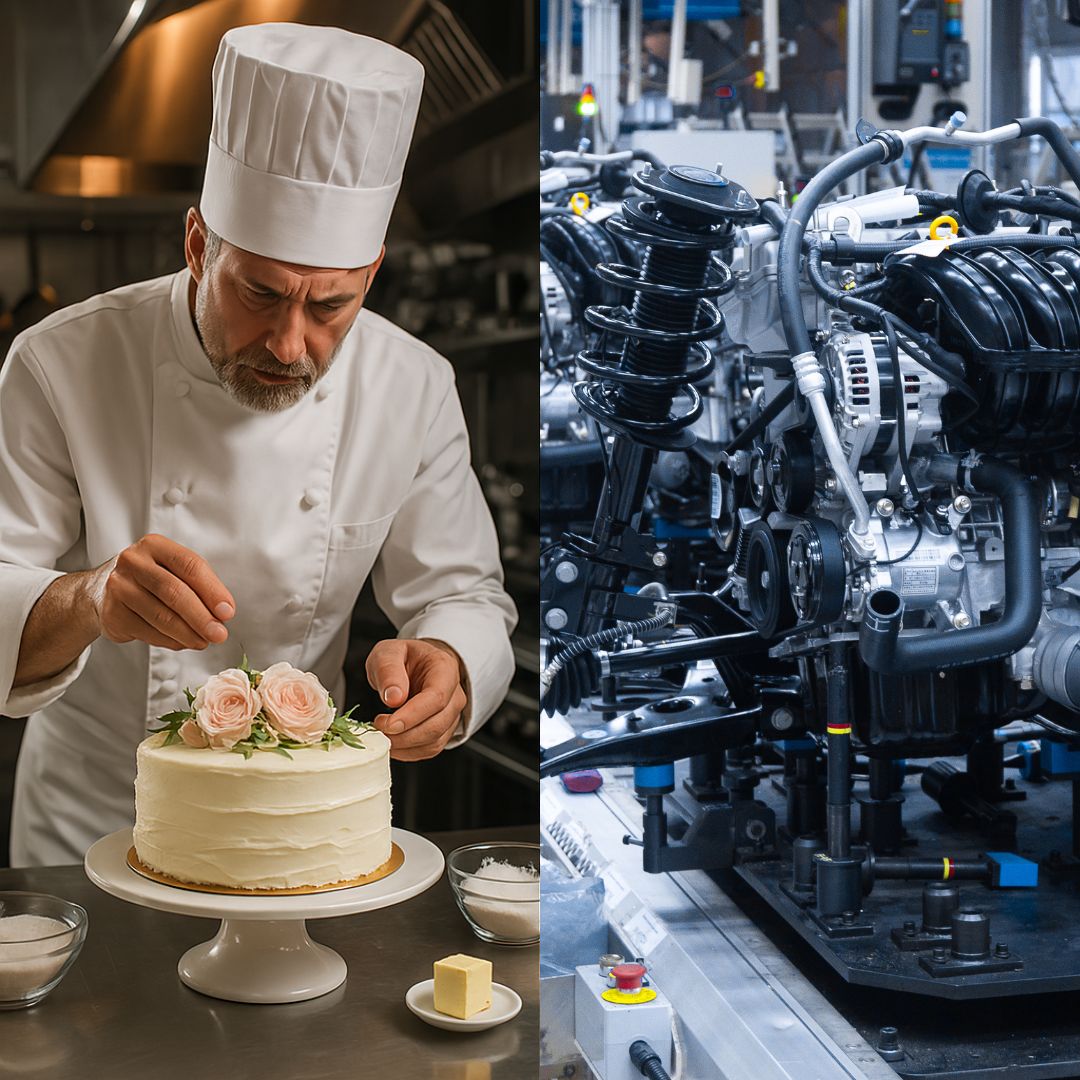
Without Data-Driven Solutions you will encounter:
1 - Unexpected Downtime: Your oven breaks down in the middle of a big order, leaving you with half-baked cakes and dissatisfied customers. Similarly, your tightening equipment malfunctions during production, causing delays and halting the assembly line.
2- Lower Quality Control: You only realise your cakes are too dry when customers start complaining, and by then, it's too late. In parallel, you only detect torque inconsistencies when defects are reported, leading to potential recalls.
3- Inefficiency: You spend hours trying to figure out why your cakes aren't rising, wasting ingredients and time. Likewise, you spend valuable time troubleshooting why certain components are not meeting torque specifications, wasting resources.
In essence, using data-driven solutions is like having a master chef guiding you through every step of baking, ensuring each cake is perfect. Similarly, in automotive manufacturing, data-driven solutions provide precise guidance for the tightening process, ensuring each screw is correctly fastened.
Solution exists! Discover a single database for the entire tightening process analysis