2. Assembly solutions
Assembly experts, such as Desoutter’s, have developed a wide range of corded and wifi-enabled assembly solutions designed to ensure that NEV assembly is safe, efficient, flexible and traceable. Several ranges of transducer-based tightening tools, for example, are equipped with torque and angle sensors to ensure that the joint is tightened using the correct tightening parameters.
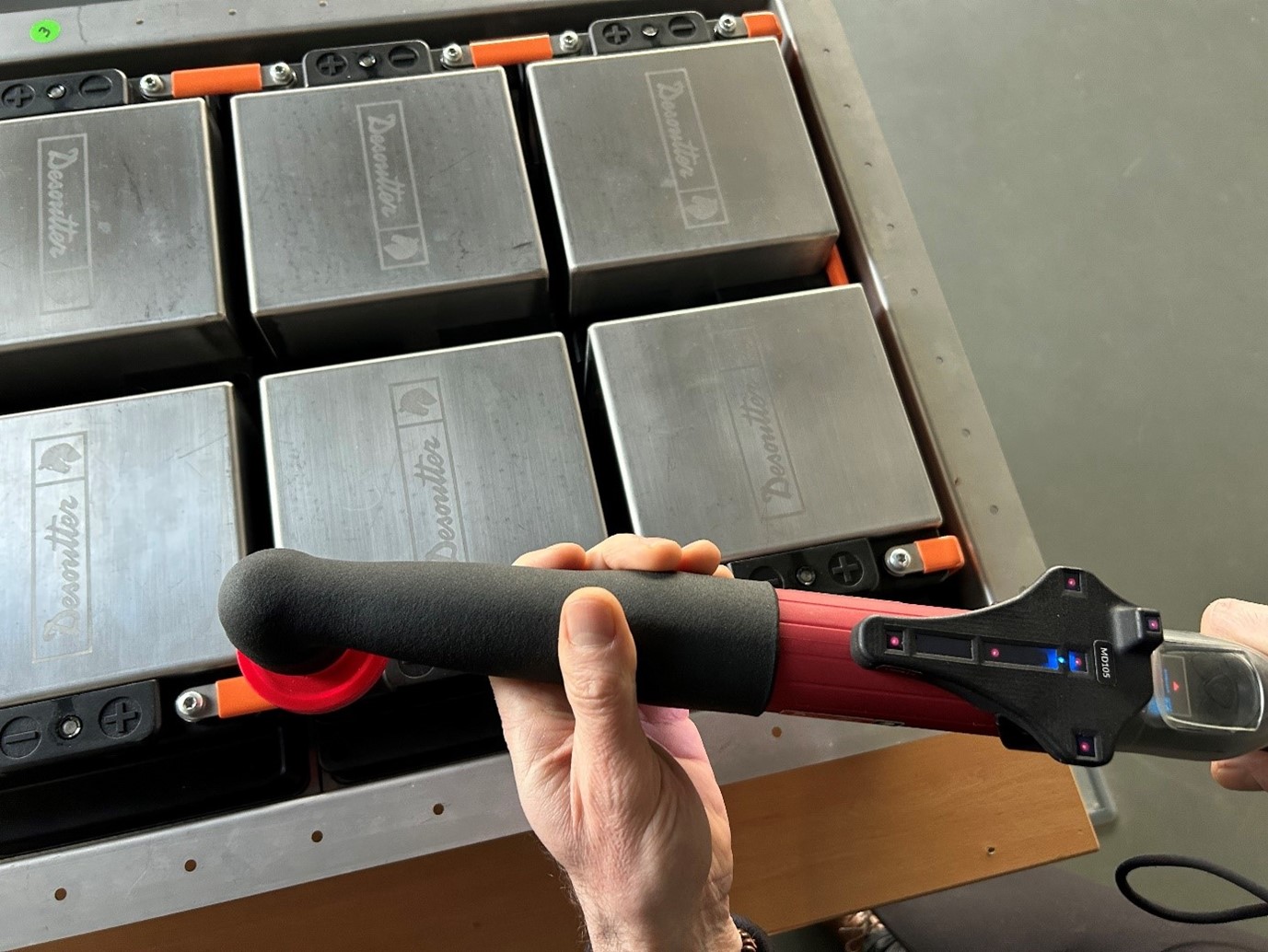 |
|
Such tools feature insulating adaptors and can be equipped with guards to minimize the risk of dangerous contact voltages, making them ideal for power busbar connection. These products for worker protection have been tested and approved by Dekra according to IEC 60900:2018, IEC 60664-1 and EN 60745-1. |
Sequenced tightening for total quality control can be achieved using worker assistance platforms:
Process control software, which guides the operator through each stage of the tightening process. One NEV application is securing the battery pack cover, which requires synchronous bolting to make sure the seal between the cover and lower casing is watertight.
Worker guidance systems that use a combination of lazer guidance and motion capture technology are being introduced to support Poka Yoke principles and deliver error-free tightening processes. Such systems eliminate operator error completely, ensuring that no bolt is overlooked and that the correct torque is applied every time.
Multi-spindle solutions,allow synchronous assembly to the defined torque: for example, ensuring that modules in battery packs are mounted with adequate clamping force to eliminate settling, so that assembled components do not warp. Multi-spindle solutions improve cycle times significantly, particularly when used in conjunction with an automated bolt feeder.
The exchange of tightening data with the higher-level control system can be assured using a smart hub in combination with wireless tools. For example, when a control system transmits the correct parameters for the upcoming tightening job to the tool, it receives the tightening results for traceability and documentation in return.
Performance, quality and other NEV assembly parameters can be monitored constantly using data analysis dashboards. There is also the option to send real-time alerts to smartphones. Detailed data analytics with real-time KPIs for performance, quality and availability swift identification of production trends for continuous efficiency improvement.
Big data analytics can also support total traceability. In the past, traceability data was stored separately and was not easy to interrogate. New big data solutions can collate and analyse data at every level of production and from any device or system, regardless of manufacturer. Automated reporting enables manufacturers and suppliers to access complex data sets at any time to obtain insights on virtually any aspect of quality and production, including:
- % nok parts / station
- average time per part / station
- % assembly errors / station
- process control alerts
- empty tool’s battery alerts
- missing parts alerts
These invaluable insights not only identify areas for continuously improving production efficiency and reducing cost, but also greatly reduce the likelihood of expensive and damaging product recalls.